Clear Ice Maker (2 Patents)
Consumer product design to produce clear ice spheres (craft ice) generally used for alcoholic drinks like high end whiskey. Advantages of clear ice is mainly aesthetic appeal, slow rate of melting and being clear contains almost zero impurities that will not impart a taste into the drink. The process of making clear ice can be done by two different phenomena. The Cascade method or Directional Freezing, we built one for each method. The unit pictured to the right utilized the Cascade method and was a very involved and complex system. First the process of making repeatable clear ice requires precise tuning of the thermal system to ensure the ice does not freeze too fast and accurate control over the impeller motor which scrubbed water across the surface of the ice sphere as it was freezing. The system used 3 capacitive touch sensors to determine how the sphere was freezing and therefore control the impeller motor TEC PWM power to keep freezing at a constant rate. The final system included a full ready to deploy firmware that auto filled/drained the water reservoir. Start sequence that would initialize a seed crystal (small starting ice block that would freeze cloudy underneath the ice sphere in order to provide a base for the clear ice to grow on. The freeze cycle a low power storage mode at the end of a cycle until the sphere was removed and finally a heating cycle to aid in removal of the ice sphere. While the product was not taken to market this provided an incredibly good experience into a full system design with industrial design, firmware, mechanical, electrical, FDA compliance, motor control and precisely tuning several of the different processes to ensure a clear sphere every time!
Main Roles: Supporting industrial design house, Mechanical design of internal components, most notably the gantry mechanism that would allow the head to lift and lower for easy sphere removal. Providing the overall software flow and testing different aspects of the software as they became ready. Leading programming brainstorming sessions to guide the programmers on how the sensitive system should be controlled. Numerous tests including fill pump PWM and impeller motor PWM sequences to ensure bubbles where not inadvertently injected into the system.
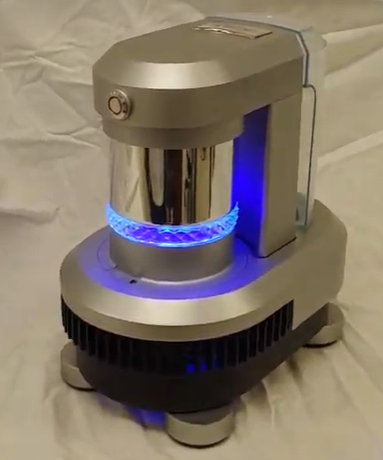